After fouling, the pumping rate of the vacuum pump will be reduced. Since there is scale between the impeller blades and on the inlet and exhaust windows, the volume of the sealed chamber is obviously reduced, and the volume of the inlet and exhaust gases is naturally reduced. When the fouling almost fills the space between the blades or the intake and exhaust windows are almost blocked with scale, the intake and exhaust volume is almost zero, and the vacuum pump loses its ability to extract vacuum.
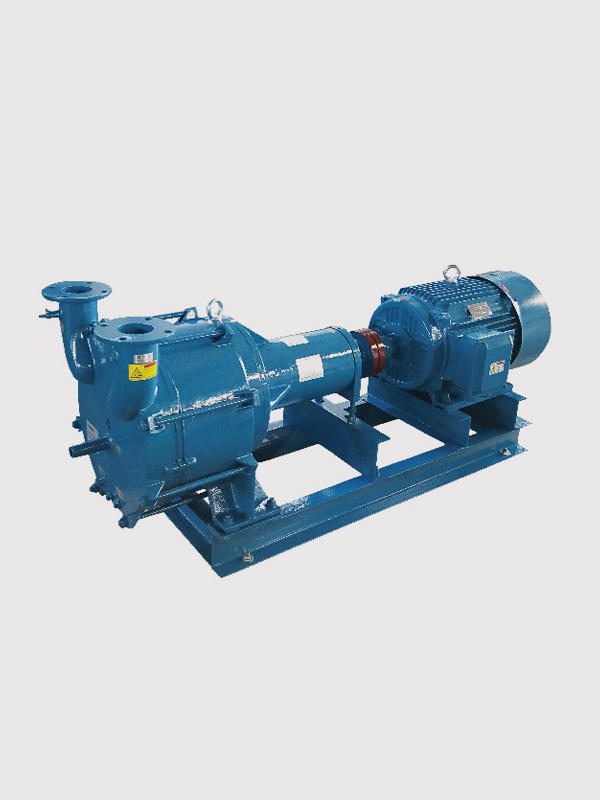
The fouled vacuum pump not only reduces the pumping rate, but also leads to higher power consumption. It can be seen from Figure 1 that due to the formation of scale, the exhaust window is reduced, and the compression ratio of the gas in the small chamber increases when it is discharged from the window, resulting in an increase in power consumption, and the power consumption is increased by about 10%.
Therefore, after the vacuum pump has been running for a period of time, although the operation of all aspects is still normal on the surface, the vacuum degree of the pumped container has decreased, and the power consumption has increased. The reason is likely to be caused by scaling.