The rotary vane pump always fails to reach the vacuum degree, or leaks and injects oil, which brings a lot of unnecessary trouble to the production. So, what is the reason why the vacuum degree of the rotary vane vacuum pump cannot be reached?
Insufficient amount of oil: Under normal circumstances, it is not necessary to connect the exhaust pipe. When pumping a large container or carrying out gas ballast for a long time, due to the large amount of gas entering the pump, a large amount of oil mist will be ejected from the exhaust port, which will reduce the amount of oil. Insufficient oil will affect the performance of the pump and even damage the parts. The elimination method is to add new oil frequently.
Contaminated oil: When the pump is used frequently, the pump oil will inevitably be contaminated by dust, moisture or other contaminants. Contamination of the pump oil can affect performance, so an oil change is required. The oil change period depends on the nature of the gas being pumped and its actual working conditions. Generally, the oil change period when the air is pumped is 1000~1500 hours when the pump is actually working.
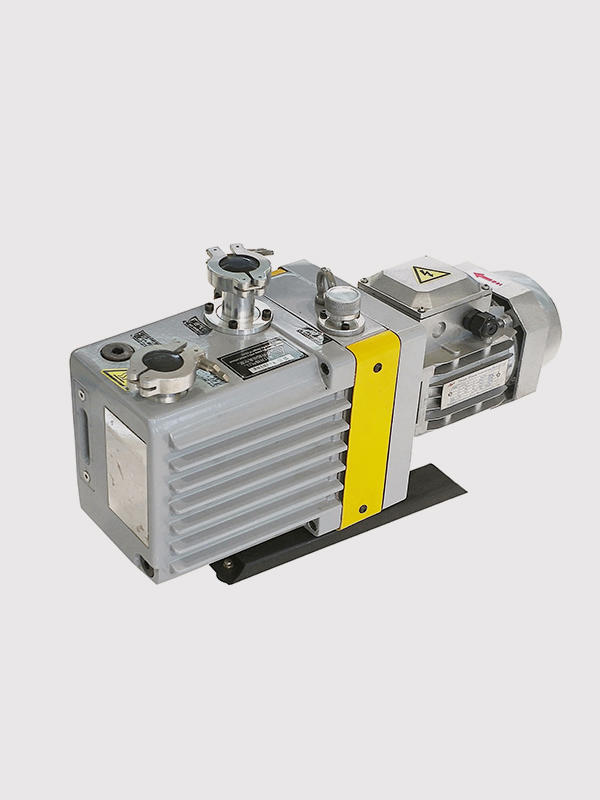
Oil changes should be performed in the following order:
1) Completely drain the old oil in the pump;
2) After the old oil is exhausted, inject a small amount of new oil (100~200 ml) from the air suction port, rinse the inside of the pump chamber, then start the pump to run for one minute, and then exhaust the injected new oil. If it is not clean, you should continue to inject new oil to rinse until the oil drained from the pump cavity is clean;
3) Add new oil according to the oil capacity specified by the pump, so that the oil level reaches the center of the oil mark, pay attention to cleaning when refueling, and prevent dirt from mixing into the pump.
Damage to the sealing ring at the air outlet: the exposed part of the pump oil has a special bowl-shaped sealing ring, and the air inlet and the rear cover are equipped with an "O"-shaped air sealing ring, which may be damaged after a long time of use, resulting in oil leakage. If the gas phenomenon occurs, the sealing ring should be replaced in time.
Exhaust valve plate damage: Oil-resistant rubber valve plates are installed at the exhaust holes of studio I and II respectively. During the long-term use of the pump, the valve plate will be deformed due to pressure and other reasons. As a result, poor sealing occurs and air leakage affects performance. At this time, the pump should be disassembled for inspection and replacement in time.
Poor sealing of the connection: At this time, the pipe joints should be carefully checked to eliminate air leakage.
The pump is dirty and dirty: whether the pump is clean or not directly affects the performance of the pump. During the use process, the pump will inevitably be dirty and dirty. It should be washed thoroughly with fresh oil, then dried and assembled carefully.
Damage to parts: After long-term operation, the wear of the stator, rotor and blades will seriously affect the volumetric efficiency. In this case, the pump body should be completely dismantled and repaired or replaced with a new one.